EVO PT®
Specification
-
Overview
- 优化定位点
- 安装扭矩独立于深度
- 支持完整的CAE设计
- 流程非常安全
- 有标准化的可能性
塑料自攻螺钉的革新
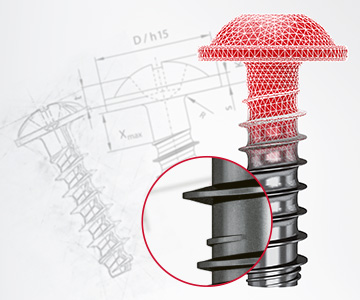
EVO PT®是在热塑性塑料自攻紧固件基础上发展革新的。这是首次在开发过程中将制造业与新型的计算机物理数模应用知识成功结合起来的创新研究。这是因为这种跨领域的研究方式使得这款新型螺钉有着极好的连接性能。
创新的螺纹形式
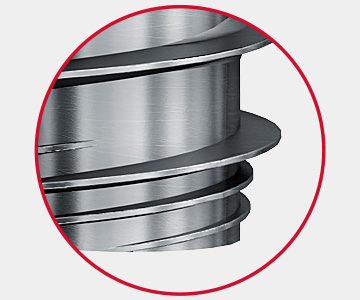
这种创新的螺纹在安装阶段产生的扭矩曲线,几乎与螺纹连接的深度无关。因此,在不同螺杆长度的安装中可以使用统一的扭矩来拧紧。
特殊的导入功能在完全紧固时在螺纹处产生均匀的载荷,因为在安装过程中螺丝会导正在预孔中间。此外,这种创新的螺纹形式可以方便地实现预孔的自对准。
EJOT EVO仿真模拟计算®
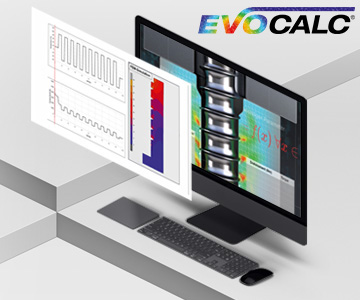
能够提供仿真模拟计算服务EJOT EVO CALC®,可以根据组件的要求计算出扭矩和预紧力。此外,在EVO PT®螺钉方面,我们提供了单独的有限元支撑组件优化。这样,在设计阶段就已经实现了节约时间和成本的效果。
CAE services - component optimisation and individual design engineering assistance
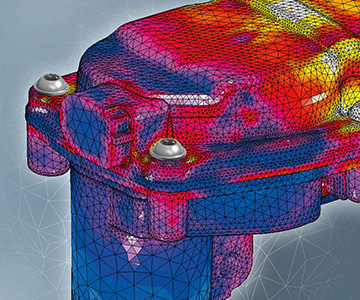
We also support you during the development phase with our CAE services. With the help of innovative calculation and simulation tools we estimate the behaviour and the effect of our fastening elements on your component under various loads and then give you the respective recommendation. It is possible to calculate the clamp load relaxation of individual screw joints and also to analyse the behaviour of the complete assembly. More...